10 Easy Facts About Alcast Company Shown
10 Easy Facts About Alcast Company Shown
Blog Article
Some Ideas on Alcast Company You Should Know
Table of ContentsAlcast Company - The FactsAlcast Company for BeginnersThe Single Strategy To Use For Alcast CompanyThe Greatest Guide To Alcast CompanyAll About Alcast CompanyThe smart Trick of Alcast Company That Nobody is Talking AboutHow Alcast Company can Save You Time, Stress, and Money.
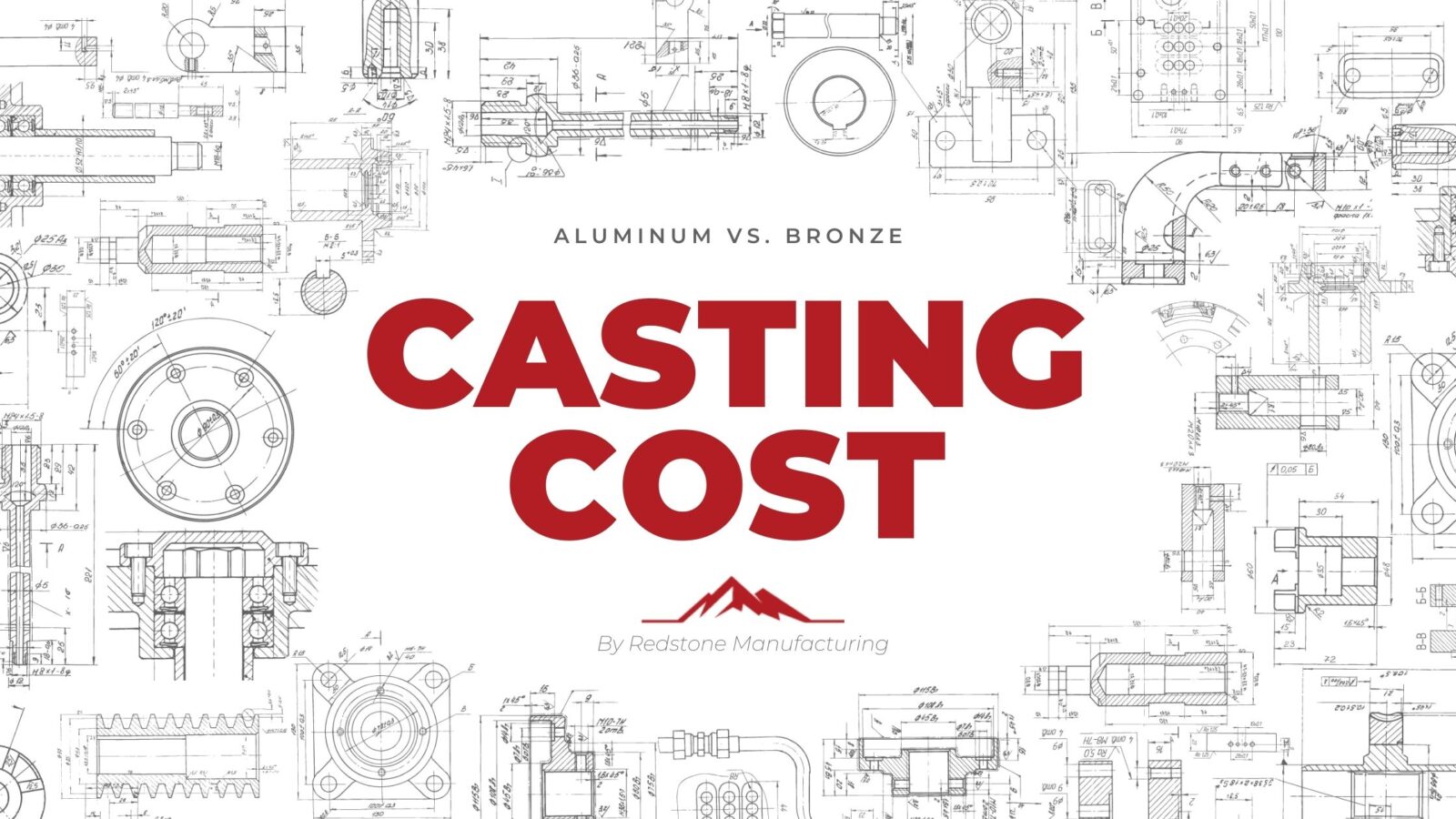
If you assume that a wrought alloy might be the very best for your task, have a look at some of our articles that discuss more about details wrought alloys, such as Alloy 6061 and Alloy 6063. On the other hand, if you believe an actors alloy would certainly be much better for you, you can discover more concerning some actors alloys in our Alloy 380 and Alloy 383 write-ups (coming quickly).
5 Easy Facts About Alcast Company Described
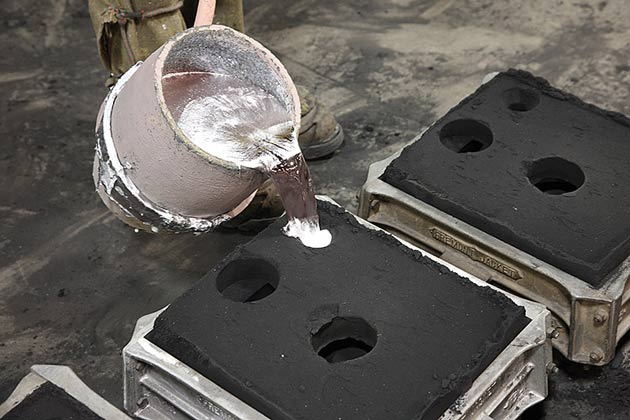
Having the experience and industry knowledge to engineer your spreadings for optimal manufacturing and top quality end results will improve the job. Making aluminum castings needs a complicated collection of procedures to attain the right results. When choosing on a new aluminum shop to partner with, ensure they have substantial sector experience and are knowledgeable about all aspects of the light weight aluminum casting procedure: style, production, product evaluation, and product screening.
(https://www.avitop.com/cs/members/a1castcmpny.aspx)The foundry needs to likewise have a tried and tested record of supplying phenomenal products that satisfy or exceed client assumptions. Quality control must additionally be at the top of your listing when picking an aluminum factory. By collaborating with a qualified factory that follows the criteria for quality assurance, you can safeguard the honesty of your item and ensure it satisfies your requirements.
Alcast Company for Dummies
By choosing a company who supplies solutions that satisfy or exceed your product needs, you can be certain that your job will certainly be completed with the utmost precision and performance. Different parts call for different manufacturing methods to cast light weight aluminum, such as sand spreading or pass away spreading.
Die casting is the name offered to the process of developing complex steel components with use of mold and mildews of the part, also known as dies. It generates even more elements than any kind of various other procedure, with a high degree of precision and repeatability. There are three sub-processes that drop under the classification of die spreading: gravity die casting (or irreversible mold and mildew casting), low-pressure die spreading and high-pressure die casting.
Despite the sub-process, the die spreading procedure can be damaged down into six actions. After the pureness of the alloy is tested, dies are produced. To prepare the passes away for spreading, it is important that the dies are clean, to make sure that no deposit from previous productions remain. After cleaning, the ejection lubrication is related to the die to make certain a smooth launch.
The pure metal, also called ingot, is included in the heating system and kept at the molten temperature of the metal, which is then transferred to the injection chamber and injected into the die (aluminum metal casting). The stress is after that kept as the steel strengthens. When the metal solidifies, the cooling procedure begins
Fascination About Alcast Company
The thicker the wall of the part, the longer the cooling time because of the quantity of interior metal that additionally requires to cool. After the part is completely cooled down, the die halves open and an ejection mechanism presses the part out. Complying with the ejection, the die is closed for the following shot cycle.
The flash is the added product that is cast during the process. This need to be cut off utilizing a trim device to leave just the primary part. Deburring gets rid of the smaller items, called burrs, after the trimming procedure. The component is brightened, or burnished, to give it a smooth surface.
The Buzz on Alcast Company
Today, top suppliers utilize x-ray screening to see the entire inside of components without cutting right into them. To obtain to the ended up item, there are 3 primary alloys utilized as die spreading product to pick from: zinc, aluminum and magnesium.
Zinc is one of the most previously owned alloys for die sites casting due to its lower expense of basic materials. It's also one of the stronger and steady metals. And also, it has superb electric and thermal conductivity. Its deterioration resistance also allows the components to be long-term, and it is among the much more castable alloys as a result of its reduced melting factor.
The Buzz on Alcast Company
As mentioned, this alloy is among the most generally utilized, yet manufactures will, at times, pick aluminum over zinc as a result of aluminum's production advantages. Aluminum is very cost-effective and one of the extra versatile alloys. Light weight aluminum is used for a variety of different items and sectors anything from window frameworks to aerospace products.
Report this page